Kayak2号艇製作記-1(ハルとデッキの仮接着まで)
Wood Duck 12を設計図から造りました(2012/8 ~ 2013/5)
今回の目的
1号艇はキットから作ったため合板はマリン合板(Jubert社製マリン合板-オクーミ材)でしたし、エポキシも正攻法でSystem Three社のエポキシを使いましたが、国内で材料を調達しようとするとマリン合板は売ってない、輸入エポキシは高価。そこで、今回は国内で安価に調達できる合板とエポキシで製作することを目的にします。
- 合板:ラワン耐水合板(Type Ⅰ)3mm厚
- エポキシ:コニシE206(あるいはE205)
これらで一体いくらで製作できるかに挑戦です。それに、色々と反省点やら改善点があるので同じ型の船を二度造れば腕も上がるだろう(ちょっと原設計に変更を加える予定)。
[1]材料と部材の準備
プライウッド
12ft(3.6m)の船を造るのに3x6の板2枚接いでもちょっと足りない。2カ所接ぐのは躊躇われたので仕方なく4x8の板を使うことにしました。購入したのは米屋材木店(三興プライウッド㈱製)、1枚¥3,015 送料¥2,500のしめて¥14,560でした。ホームセンターにあるものより裏表とも大変綺麗で抜けもない上質な板でしたが、3x6基準でできてる日本の家では4x8は取り回しが大変。アメリカン・サイズなんだなぁと実感しました。
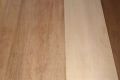
エポキシ
エポキシはコニシE206W。購入したのが冬だったので低温用(W)ですがデータシートによれば結構ゲルタイムが長いため気温が高くても可使時間に問題はないようですし、夏用(S)より粘度が低いので好都合です。Amazonで¥7,270でした。「土木建築用エポキシ樹脂」というのが笑えます。
設計図
CLCから設計図を購入($99、送料込¥8,118)しましたが、ロフティング(座標上ポイントを記した表から部材の形を板の上に描いていく作業)が必要かと思っていたら、CAD出力と思われる97cm x 400cmあまりのロール紙二枚に印刷された原寸型紙が送られてきました。
ロフティングの手間は省けるけどこの薄い型紙からどうやって板に転記したものか。マニュアルには「パーツごとに切らないこと。原寸図を板に重ね、ラインに沿って錐で穴を空けていきそれをつないで滑らかなラインを出せ」だと。プチプチやるのは気が遠くなりそうなので、型紙下にカーボン紙敷いてトレースしていくことにしました。
フレームの位置やスティッチする銅線を通す穴の位置まで印刷されているので大変ありがたいことです。もっとも設計図によれば「まず4x8を2枚接ぎ、対角線でカットしてパーツを転記していけば効率的に木取りができる」そうですが、4x8を2枚平らに置いておけません!
カット
ボトム・パネルなど左右2枚の部材は板を中表に重ね、2枚いっぺんに丸ノコで転写ラインぎりぎりを切っていきます。下に敷いた発泡スチレンごと切ってしまえば切り口も滑らか、板もたわまず正確に安全に切れます(ただしカーブのきついところは丸ノコでは無理。一度気を抜いてたらキックバックしちゃってヒヤリとしました)。
カーブしたラインはさすがに丸ノコでは切れないのでジグソーの出番です。このジグソー、小型でストロークも16mmしかないのですが薄い合板切るには充分。刃が下に敷いた発泡スチレンを突き抜けちゃうと困るので刃をちょん切り短くして使いました。
ジグソーは僅かずつ進行方向を修正しながら切っていくため、どうしても(腕のせいか?)切り口がデコボコになるので、後で修正するときにはまず鉋かけてからペーパーで滑らかにする必要がありました。パネルのエッジを眺めスムースで綺麗なカーブを描いているように修正して部材の完成です。おっと、銅線通す穴も空けておかなくちゃ。
切り出されたパーツ
出来上がった部材を船の形に並べてみました。これら以外にバルクヘッド、トランサム、ハルとデッキのフレーム(スティッチ後撤去)が各3枚、コックピットのコーミング、ハッチ用パーツがあります。今回は3mm合板なのでバルクヘッドには補強材を取り付けます。
[2]パネルの接合
使用する3mm合板をスカーフジョイントで接合するのは諦めました。表材が薄いため接着面が余りに脆いし、スカーフ・ラインを直線にできる自信がない。代わりに採用したのはファイバーグラスによるバットジョイントです。
まずパネル下にプラフィルムを敷き、下の作業台にくっつかないようにしてあります。接合するパネルが動かないように固定し、エポキシで接着、その上に置いたファイバーグラスにエポキシを浸潤して補強、その上に更にプラフィルムを貼り気泡をスキージで押しだし、重しを乗せておくとツルツルに仕上がります。
タックフリーを待って余分なファイバーグラスをナイフで切り取り、プラフィルムを剥がして出来上がりです。今回のエポキシは冬用なのですが、ポットタイムは室温27℃で30分近くありますし、タックフリーまでには4~5時間かかりました。
スティッチ用治具
前作では、スティッチの反省として上パネルが下パネルに落ち込み重なっちゃうというのがありました。これを避けるための方法として井賀さん製作のカヤック・マニュアルに「パネルとパネルの間に(アイスクリーム・スティックみたいな)板きれを差し込んでスティッチしろ」とあったので、これを参考に治具を作りました。外側から見るとこんな具合。
木片では強度を求めると厚くなるので金属にして、裏側はパネル位置がずれないように当て木で押さえ込んでおく。こんな治具を9個(10個作ったのだけれど一つは金属片を叩き込むときに割れちゃった)作り、ボトムパネルとサイドパネルのスティッチの際、特にバウの部分に使用する予定です。
使ったのは3cm長の丸棒、薄い鋸で金属片を差し込む切れ目を入れ、きつきつで入ったのですが念のためエポキシで接着してあります。この金属片はボルトを留めるナット代わりのものですが、薄く強度もありうってつけでした。グラインダで金属片真ん中に切れ込みを入れて完成。果たして効果の程は?
(追記)この治具、丸棒を動かしてやると自然とパネルが上手い具合に合わさってくれます(self-alignmentなんて呼ぶそうですが)。丸棒はエポキシが接着しないプラスチック製のものの方が良かったですね。
[3]デッキのスティッチ
まず前後デッキパネルをスティッチします(ハルを先に造っちゃうと作業場所がなくなるので)。デッキ前部には大きな反り(膨らみ)があるためフレームを配置するのですが、前後パネルをスティッチしただけでも結構なキャンバーがつきます。
前後パネルに加えその両側にシアー・パネルをスティッチ、4枚のフレームでデッキ形状を維持しています。シアー・パネル両端は尖った角のようになっているのでこれを折らないように作業するに気を使います。縫い合わせるパネル同士の内側をベベルカット(斜めに削る)してあるため、パネル同士は外側で接しキチンと隙間なく合わさっていますが、当然内側は隙間が空いています。
接着のためにはこれで良いのですが、ここには後でエポキシパテを充填し隙間を埋めます。試しにスティッチ治具を挟み込んでみましたが、パネル同士の接合具合(alignment)を維持するのに有効でした。治具を動かしてやると上手い具合にパネル同士が動いてくれます。
使っているのは3mmラワン合板ですが、4mmオクーメ材に比べるとヤワです。運ぶのにも気を使うし、スティッチしていると力がかかる箇所の隣が変にたわんだりしてマリン合板のようにスムースな曲線が出にくいですね。もっとも全ての箇所を縫い合わせればそんなことはないのですが。
前から二番目のフレームは一番キャンバーの強い箇所でデッキの膨らみを造っています。デッキのフレームはこれも含め全て撤去することになっていますが、このフレームを撤去するとやっぱり合板が元へ戻ろうとしてハルとの接合時、デッキをギリギリと縛り上げないとハルと合いません。そこでこのフレームだけは残し、空けた穴の先にハンモック様の物入れを造る予定です。コックピットより先なので足の邪魔にはならないし、ビルジポンプやもやいシートを入れておくのに手の届くところの方が都合がよいと思われます。
曲面をサンダーで研磨するには
ファイバー・グラッシング前に合板全体を研磨し、グラッシング後はエポキシの研磨作業が待っていますが、平面を研磨するのに使うサンダーで曲面を研磨するのはそもそも無理がある。でも手研磨はシンドイので何か方法はと探していたら、ありました、その名も「スポンジ・オーピタル・サンダー」。創意工夫に富んだ治具やら道具を考案なさっていますが、サンダー使ってもどうぜ面がダレルならいっそのこと徹底してダレテしまえば曲面も研磨可能とのこと。真似してランダム・オービット・サンダーに厚さ5cmほどのスポンジを挟んでみました。手頃な材がなかったのでSPFの丸面取りしてある角に押しつけて研磨してみたところ、スポンジが曲面にそってつぶれて丸面が平らになったりはしませんでした。これ使えるかも(ただし、集塵穴がないので集塵機が使えません。うむむ、スポンジに穴空けるか?)。
エポキシ着色
今回のラワン合板、表面は仕上げが綺麗ですがどうも色味が・・・いっそのこと裏面を外側に出しちゃおうかと思うほどです。合板をステインなどで着色することがまず思い浮かびますが、板に何か塗っておくとエポキシと木部の接着性を損なう恐れがあります。油分の多いチークやオークではエポキシによる接着が難しいというのを読んだことがありますので、ステイン以外でもカラーオイル、シェラックなどで合板表面を着色するのは躊躇われます。
今回使用するエポキシは淡黄色なため、なおさら合板の黄色味が勝りそうなので、エポキシに着色することを考えてみます。エポキシ着色剤は製品として市販されていますが、色数も少なく高価。何か方法はないかと検索してみたらすぐにヒットしました。「エポキシ系接着材の着色について!!!」と言うブログです。レジンでスイーツを作っている方のようですが、エポキシの透明度も損なわずかつ綺麗に着色できるものとして推奨されているのがなんと油絵具!ちょっと信じられない気がしますが、やってみないと始まらない。そこで合板片に油絵具を混ぜたエポキシを塗布してみました(減法混色ですから黄色+赤で茶色、黄色+黒で緑になるはず)。
ごらんのように透明度を保ったまま色のついたエポキシが出来上がりますし、赤味を帯びた色合いになりました。ただ、合板もエポキシも黄色が淡いため赤(ローズマダー)が勝り赤いジェリービーンズみたいな色になってしまいました。狙いとするOkoumeの色を出すにはまだ試行錯誤が必要ですが、簡単にエポキシを着色できることが分かりました。
[4]ハルのスティッチ
ハルのスティッチに取りかかります。まずボトムパネルのスティッチからですが、設計図に4枚のフレーム位置が記入されていたので(キットにはこれが無かった)正確に位置を決められます。4枚のうちバルクヘッドだけは撤去しないのであらかじめエポキシによる防水加工を施してあります。バウとスターンは捻ってカーブを出すためお湯で湿らせ、曲げやすくしてからスティッチします。
次にサイドパネルをスティッチしていきますが、ここで経験を活かしてバウとスターンではベベルカットをほんの僅かに抑え、加えてサイドパネルが下に落ち込みボトムパネルと重なってしまわないように治具を挟み込んでスティッチします。僅かに隙間が空いてしまいますが、パネルが重なるよりは良いし、この隙間はエポキシを充填してしまえば目立たなくなるでしょう。治具を使ったおかげで前作より設計図通りの型に仕上がったのではないかな。
[5]仮接着とドライ・フィッティング
ハルにデッキを乗せ仮組し不具合が無いことを確認してから、デッキおよびハルのパネルをエポキシで仮接着(タック・ウェルディング)します。写真はタック・ウェルディングの様子。すでにチョン付けしたエポキシが硬化した後。パネル接合面内側のベベルカットした部分に接着剤が入り込んでいればそれでOK、この後エポキシ・フィレットを乗せ本接着しさらにファイバーグラス・テープで補強します。
銅線だけでスティッチしたパネル同士をエポキシで接着するのですが、あくまで仮の接着なので銅線部分を飛ばし(くっついて抜けなくなると困るので)パネルとパネルの内側の隙間にエポキシをすり込みます。この状態で再度ハルとデッキを組みたてそのままエポキシを硬化させれば、ハルとデッキそれぞれの形が正しく固定されると言うわけです(ドライ・フィッティング)。
正確に木取りされていても合板の曲がり具合のため、ハルとデッキがピッタリ合うと言うことはまずありません。バウ付近はハルが膨らんでいるし、中間部分は逆にハルが内側にへこんでいます。膨らみは荷造りベルトやラップで押さえ込み、へこんだ箇所はスクレーパーなどを差し込んで外に出っ張らせながら、ハルとデッキをスティッチしていきます。前作ではどうしても上手く合わなくて、仕方なく削ったり切ったりした箇所があったのですが、さすがに今回は二回目、なんの問題もなくドライ・フィッティング完了です。今後はエポキシ作業になりますのでページを改めます。